Corrosion Protection
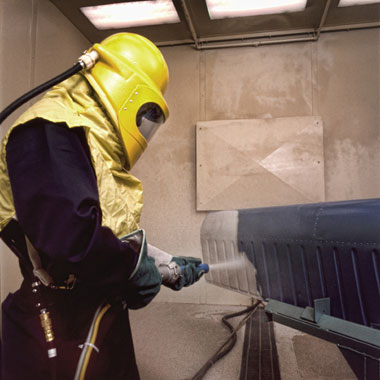
Corrosion is the gradual destruction of material, usually metals, by chemical reaction with its environment – this generally means the electro-chemical oxidation of metals in reaction with an oxidant such as oxygen. Rusting, the formation of iron oxides is a well-known example of electrochemical corrosion. This type of damage typically produces oxides or salts of the original metal and corrosion degrades the useful properties of materials and structures including strength, appearance and ability to contain a vessel’s contents.
Many structural alloys corrode merely from exposure to moisture in the air, but the process can be strongly affected by exposure to certain substances. Corrosion can be concentrated locally to form a pit or crack, or it can extend across a wide area more or less uniformly corroding the entire surface. Because corrosion is a diffusion-controlled process, it occurs on exposed surfaces and as a result, methods to reduce the activity of the exposed surface, such as passivation and chromate-conversion, can increase a material’s corrosion resistance.
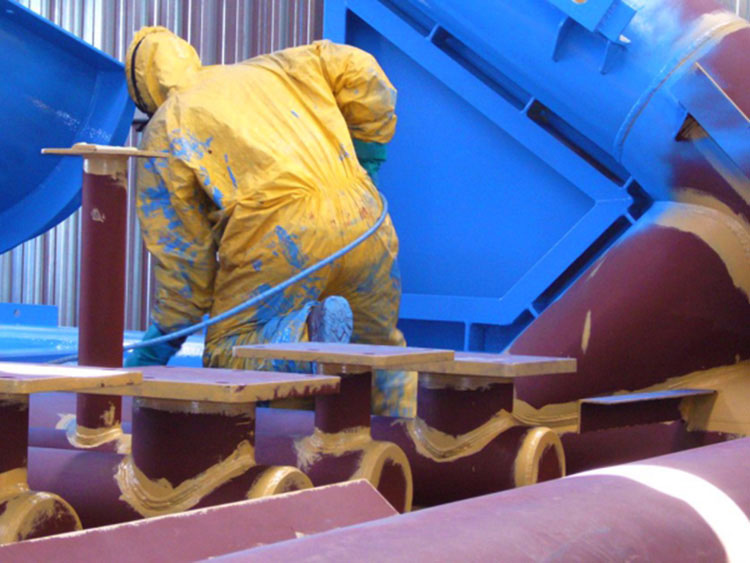
PAINTING
Probably the most widely used system of corrosion protection is by painting the metal surfaces at risk. The advantage of painting is that the protection is relatively convenient to apply and paint can be tailored to suit a specific duty.
Paint can be engineered for convenience of decontamination and provide a degree of surface protection against the environment, in addition to the required corrosion protection and it can also offer a decorative appearance and allow for ease of equipment identification.
McM has the capability and expertise to provide corrosion protection systems to internationally recognised standards.
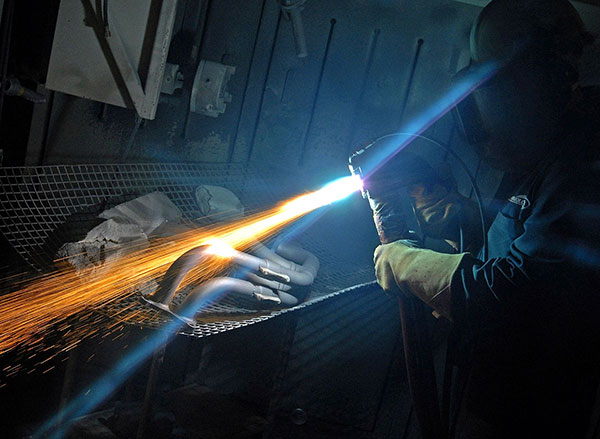
THERMAL SPRAY APPLICATIONS
Thermal spraying is a process that has been used successfully throughout industry since about 1910 and involves the propulsion of metallic and non-metallic compounds (in either wire of powder form) onto prepared substrates. There are typically 6 different thermal spray processes – McM Blasting and Coating uses the combustion wire metallising flame spray and wire arc spray processes to provide zinc or aluminium corrosion protection for their clients.
The metallising (or combustion wire) process is a process whereby compressed air draws a solid wire through a spray gun where the wire is melted in a nozzle in which oxygen and a fuel gas (either acetylene or LPG) combine at temperatures around 2700 degrees Celsius. The molten metal is then projected onto the prepared substrate adheres to it at high velocity.
Electric arc spray is a form of thermal spraying where two consumable metal wires are fed independently into the spray gun, the wires are electrically charged and an arc is generated between them. The heat from this arc melts the incoming wire, which is then entrained into an air jet from the gun and the resulting molten feedstock is then deposited onto a prepared substrate.
Currently McM uses thermal spray processes for the corrosion protection of amongst other components, subsea drilling equipment and risers.